GENERAL
Once all millwork drawings, materials, colours, and so on, have been signed off on, it’s anywhere from 4-8 weeks from sign-off to the point at which everything is ready to go and all the parts and pieces are finished and available. (Everything we do for you is created specifically for you — we don’t pull your cabinets from a shelf.) That said, please keep in mind that other factors do play into the overall time: We are only one piece of the puzzle.
Yes, we are.
Of course! We fit the small jobs in between the big jobs. However, when we’re working on the really large jobs, we can end up with a very tightly booked schedule, so it is best to call us and ask if we have the time to fit in your small job.
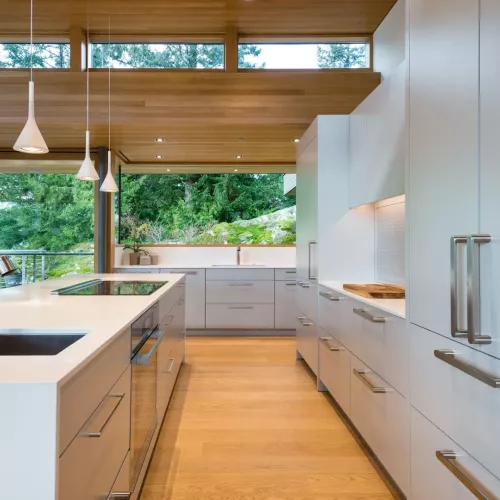
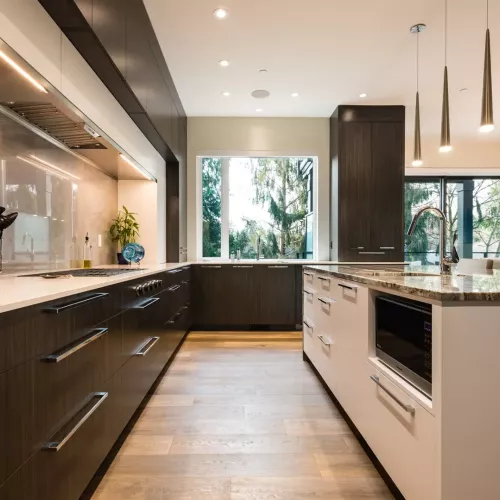
PREPARATIONS
No – we can do the drawings for you. Knowing what you want is key and if you’re not sure, we can help you identify exactly what that is.
Yes, but we will need to draw up separate millwork specific plans that will likely be much more detailed than the project renderings done by your designer or architect. We also take our own measurements of project spaces to avoid any errors.
A good designer can be very helpful in ensuring that your project realizes its full potential and more. If you are short on time, a designer is a great option as finishes, fixtures, and design decisions are very time-consuming and daunting.
We are more than happy to help you design your space – we have an in-house design team who can help you throughout your project, whether it just be with small decisions like picking and ordering handles and their sizes, or whether you want help with space design, colour design, fixtures and finishes, or more. For our many clients who do not have a designer working with them, it is a natural part of our initial on-site meetings, drawing process, and material choice meetings to at least help with maximizing their space design.
A word of caution: while the terms “designer” and “decorator” are sometimes used interchangeably, it’s important to know the difference. Decorators are primarily concerned with colour, finish, texture, and the ways in which they complement one another within the space. Designers approach their work from a space design point of view first, and work their way out to colour, finish, texture, and the ways in which they complement one another within the space.
That’s fine, though do reach out and get us involved as early on as possible.
It’s possible, yes, particularly for small projects. For anything more than small scale renovations please be aware that if this is the route you choose, you will be responsible for management of the entire project, excluding our part in the process. Doing this requires a lot of time, effort, decisions and knowledge.
Absolutely. The number one thing we need from you is for you to tell us up front, in as much detail as possible, exactly what you want to end up with. We will give you a sign off sheet which shows you all the information we need before your millwork can go into production (appliance specs, colour choices, etc) – please use this as your guideline throughout the pre-production process.
We will also rely on you to let us know immediately about any concerns you may have, to make decisions quickly, and to pay promptly. If you are under a strict timeline always try and be aware of long deliberations regarding design decisions like cabinetry paint colour choices as they can cause your project to be bumped in our production schedule if they are not made promptly.
COST
We begin with an estimate. The more details you can provide, the more accurate our initial estimate will be. As the design develops, we revisit costs. Once we establish that we’re in the right ballpark and both parties are comfortable proceeding, we come up with a design. (For more info on our process go to OUR PROCESS – Design, Build, Install).
To put it another way: While the design is fluid, so is the price, since the price will vary with material choices, construction methods, and other factors. However, we are very transparent with how we price our projects and we will always tell you up front when a material or style choice is going to create additional costs for your project. Before any production begins you sign off on both materials and price, so we are always on the same page.
The truth is, that’s nearly impossible to answer without defining details about a given project. Why? Let’s think of some of the variables. What material? How much is needed? How tall are the ceilings? Are there display cabinets with fully finished interiors? Does your design require specialty assembly methods? Does the space have unique architectural details that need to be contended with? All of these factors, and many more, will affect the “average” cost of a kitchen.
A great way to think about cost is to figure out how much your total budget will allow. For instance, if you want to renovate your kitchen, telling us the total amount you want to spend for the whole project is the best way to get an idea of what we can do for you. We price all of our millwork on a room-by-room basis using an Excel pricing spreadsheet, so you can see the complete financial breakdown. We respect your budgetary parameters and will give you the absolute best options for your price range, telling you exactly what you can do within those boundaries.
Sorry, it’s not that simple – we wish it were. While we work with all budgets by trying to scale project costs to fit our client’s budget and helping them choose materials and designs that will fit within their budget, this does not mean that we ever compromise the bespoke quality for which we are known. A custom kitchen will cost more than box store options, so if you are looking to pay a box store price then, unfortunately, custom work might not be right for you.
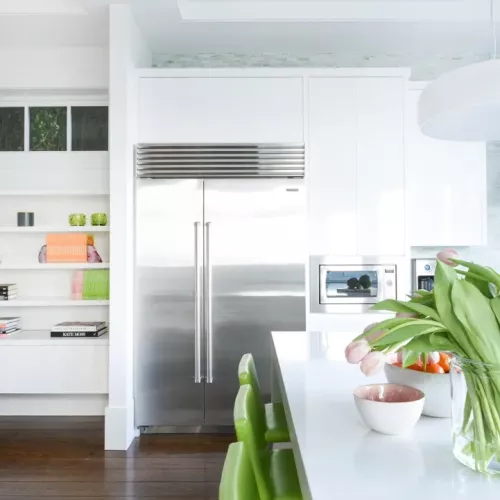
ONE SIZE DOESN'T FIT ALL
quick tip
Your space will never be plumb, flush or straight – this is why each aspect of our process involves a great deal of collaboration, precision, and problem-solving. In contrast, “one size fits all” cabinetry is about as likely to fit your space well as a “one size fits all” suit or dress is to show you off on a night out.